Logistics - Control of trucks during their stay in the company
Yard Management System - Yard control, Scheduling and Dock Management
This software allows the control of the trucks and transport vehicles during the time they are inside the company's yard for shipment or pick-up of cargo. The control includes several steps such as freight scheduling, weighing, loading, and unloading.
The process starts with scheduling the freight per day, according to the calendar shown in the image next to it.
When the transport arrives at the company, a movement record is created and the system generates a barcode card that will be used at all stages of the process.
The truck is weighed on the entrance scale and the weight is checked with the invoice. The weight of the scale is automatically captured for the system and the invoice is imported into the system through the xml file.
In the next step, the truck is sent to a parking lot, where the checklist of the vehicle, cargo, documentation and accessories is performed. In the driver's history you can check the scores obtained in your previous freight.
If approved on the checklist, the vehicle is sent to one of the docks. After the arrival, a new checklist must be filled in and the loading or unloading process is carried out.
Once the process is complete, the vehicle leaves the dock and is again weighed on the exit scale. The whole process has several controls, approvals and validations. The system allows the achievement of several indicators in real time.
Below are some of the reports and features developed in this module:
When the transport arrives at the company, a movement record is created and the system generates a barcode card that will be used at all stages of the process.
The truck is weighed on the entrance scale and the weight is checked with the invoice. The weight of the scale is automatically captured for the system and the invoice is imported into the system through the xml file.
In the next step, the truck is sent to a parking lot, where the checklist of the vehicle, cargo, documentation and accessories is performed. In the driver's history you can check the scores obtained in your previous freight.
If approved on the checklist, the vehicle is sent to one of the docks. After the arrival, a new checklist must be filled in and the loading or unloading process is carried out.
Once the process is complete, the vehicle leaves the dock and is again weighed on the exit scale. The whole process has several controls, approvals and validations. The system allows the achievement of several indicators in real time.
Below are some of the reports and features developed in this module:
|
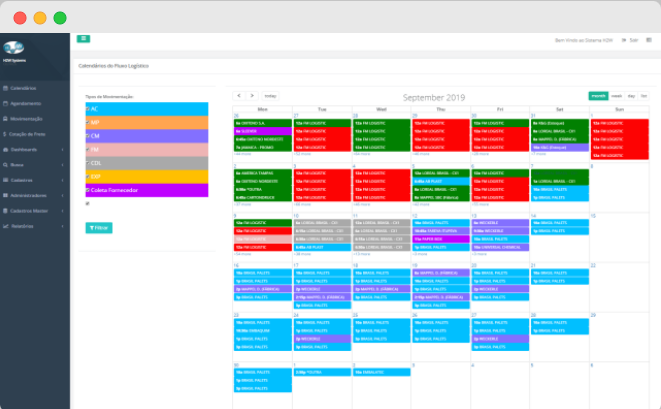
Freight scheduling calendar.
Screen that allows the visualization of the vehicles that are in each dock and time in which they passed through each step of the process.
Report regarding the expedition grid.
Logistics - Cargo Plan
Cargo Plan - Optimization for the Palletizing of Products and Organization of Pallets in Transport
Software that optimizes the use of pallets, trucks and containers by calculating the best pallet to be used according to the dimensions of the products and better means of transport according to pallets, load weight and freight costs.
This module was developed with the objective of facilitating and reducing the time required with the calculation of the load plan. The system captures the data of ERP's budgets and requests to perform the calculations.
At first, the system calculates the best pallet according to the dimensions of the product, considering boxes and reels. For the coils, the system calculates the coil diameter, considering linear meters and weight.
After this, the system considers possible pallet restrictions per customer or products has several rules to optimize the organization of products on pallets and consume as little space as possible in transportation. All rules were created according to the requirements and way of working of the client.
The system provides the production operators with the arrangement of the coils on the pallet, according to the calculation performed, according to the image on the side.
After defining the pallets that should be used, the system seeks the best transportation, considering the lowest cost to send the volume to the given destination.
Once the transport, truck, container, and available size have been defined, the system displays the schema of how pallets should be allocated in the transport, optimizing space.
Below are some features of this module:
At first, the system calculates the best pallet according to the dimensions of the product, considering boxes and reels. For the coils, the system calculates the coil diameter, considering linear meters and weight.
After this, the system considers possible pallet restrictions per customer or products has several rules to optimize the organization of products on pallets and consume as little space as possible in transportation. All rules were created according to the requirements and way of working of the client.
The system provides the production operators with the arrangement of the coils on the pallet, according to the calculation performed, according to the image on the side.
After defining the pallets that should be used, the system seeks the best transportation, considering the lowest cost to send the volume to the given destination.
Once the transport, truck, container, and available size have been defined, the system displays the schema of how pallets should be allocated in the transport, optimizing space.
Below are some features of this module:
|
Generation of the load plan quickly and automatically, with data captured from the ERP. |
|
Optimization of pallet spaces, calculating better pallet and organization form for each case. |
|
Optimization of spaces for transport, calculating better form of organization.
|
|
Generation of indicators related to optimizations and costs by period, customer, carrier, etc.
|
Load plan.